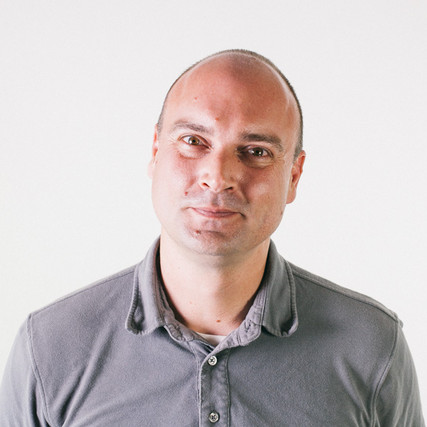
I help build technology companies. Sometimes I found them, sometimes they found me. Whichever it was, I learned a ton about building companies, developing technology platforms and scaling teams. I like to work at the intersection of technology and operations. Finding the optimal balance between these two areas to grow and scale a business is what gets me excited.
I am CTO at Shapeways. We acquired Shapeways after its bankruptcy and restarted the business. Shapeways focuses on production-grade digital manufacturing and operates in the domain between prototyping and mass-production enabling low volume production to various manufacturing industries. We help our customers with production needs traditional manufacturing companies cannot meet whether it is gap production, overflow production or mass customization. Our agile production technologies removes many barriers for our customers.
Previously I was managing director US at Hubs – formerly known as 3D Hubs. Hubs is one of the pioneers of distributed digital manufacturing using 3D printing, CNC and injection molding through a global network of manufacturers. Hubs was acquired by Protolabs (NYSE:PRLB) in January 2021 for $280M.
Before that, I was COO and employee #1 at Karma working on building a distributed wifi network using shared LTE hot spots as our back haul. We had 150k+ subscribers and we were the first wireless operator in the US to offer unlimited mobile data. Karma was part of Techstars.
I co-founded and was COO/CTO at Shapeways. Shapeways was one of the first online 3D printing and on-demand manufacturing services who made 3D printing accessible to anyone. Shapeways had over 100,000 shops, 1M+ users and we printed 24M+ parts shipped to almost every country in the world.
I started my career as a white hat hacker for Ernst & Young IT audit services before I moved on to the world of technology startups. During college, I worked for a local web development agency as a full stack developer.
In my spare time, I love nurturing my orchids, bonsai and tropical fish. Also, Iām a part-time audiophile and enjoy listening to my collection of CDs and records.
I hold a dual major bachelor’s degree in Computer Science and Business Administration from Fontys University in Eindhoven, The Netherlands.
This is my playground. I write a lot, sometimes it ends up here. I cover a wide range of topics with my own biases and make no pretense to be authoritative in any of them. Caveat emptor.
You can contact me at [email protected] or on LinkedIn. Feel free to shoot me an email. I am always open to chat!
Latest blog posts:
- Bring your own (Fire) TV
- Skipping the news cycle
- Work-life balance at a startup
- Company or office politics are poison
- Privacy for the sake of privacy
Interviews:
- CNBC
- Wired
- Wired #2
- Graphic Speak
- (in Dutch) FrankWatching
- (in Dutch) nu.nl
- (in Dutch) Telegraaf
Panel: 3D/DC
Patents:
- Weight-based identification of three dimensional printed parts (US Patent # 9,821,519, granted)
- Systems and methods for three dimensional printing (EU #EP2734946B1, granted)